Fluorite is a non-renewable mineral resource. Its chemical composition is calcium fluoride (CaF2), which is an essential upstream basic raw material for the fluorine chemical industry chain. Concentrated sulfuric acid and acid-grade fluorite fine powder are commonly used in industry to extract fluorine. . It is widely used in many important industries related to the national economy and people's livelihood, including emerging industries such as new energy and new materials, as well as traditional industries such as refrigeration, building materials, smelting, optics, ceramics, glass, etc. realm of meaning. Through beneficiation and processing, high-grade minerals can be obtained, and resources can be efficiently recycled and utilized. Considering the actual situation of the mines, there are four types of fluorite ore flotation process methods that will be different.
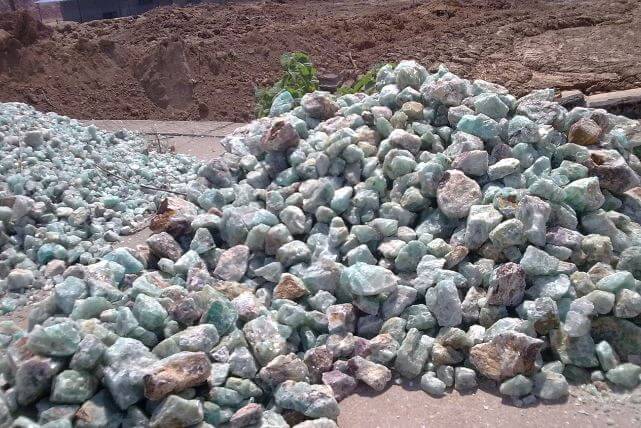
Fluorite, generally symbiotic with quartz, barite, pyrite, etc., is brittle in texture, high in melting point, non-toxic, and has a variety of bright colors, common ones are purple, green, blue, etc., in chemical, building materials, cement, Glass, ceramics, cast stone and other fields are widely used. Among them, domestic fluorite mines are famous in the world, especially the Wuyi area in Jinhua, Zhejiang, which is also known as the “Hometown of Fluorite”. Due to the very unique chemical properties of the fluorine atom, its use cannot be replaced. Therefore, at the policy level, my country has positioned fluorite as a “valuable resource that can be exhausted and non-renewable”, and fluorite is called “the second rare earth” in the industry.
1. Quartz-Fluorite Ore Flotation
It is mainly composed of fluorite (up to about 85%) and quartz, with only a small amount of calcite, barite and sulfide. Reducing silicon in concentrates is the focus of this type of ores, and the requirements for silicon content vary according to different usage requirements. In the process of beneficiation, grinding is a factor that greatly affects the flotation of quartz-type fluorite ore, and it is necessary to dissociate the quartz and fluorite monomers through grinding. Since most quartz-type fluorite ores have conjoined bodies of quartz and fluorite, the grinding particle size is too fine, which will lead to excessive crushing of fluorite and affect the recovery rate. Therefore, the stage grinding process is generally adopted, which not only reduces the silicon content of the concentrate product after fluorite flotation, but also increases the recovery rate of the fluorite concentrate. Using the process flow of stage grinding stage flotation, high-grade fluorite concentrate can be obtained after multiple selections.
This type of fluorite ore can be divided into two types, coarse-grained and fine-grained, according to the embedded characteristics of useful minerals.
- Coarse-grained embedded fluorite is easy to select, using fatty acid collectors, ore slurry adjuster as sodium carbonate, quartz inhibitor as water glass, and high-quality fluorite concentrate can be obtained through a coarse-multiple refining process.
- The flotation reagents of fine-grained embedded quartz-type fluorite ore are the same as those of coarse-grained embedded quartz-type fluorite ore. However, due to the fine particle size embedded in the target minerals, it is necessary to strengthen the grinding, and the staged grinding stage is adopted for the separation process.
Quartz-fluorite type ore beneficiation process: raw ore crushing-grinding-roughing-rough concentrate regrinding-multiple selection;
2. Calcite-fluorite ore flotation
The main minerals of calcite-fluorite type ore are fluorite and calcite (the content is as high as 30%), some contain a small amount of quartz, and sometimes quartz-calcite-fluorite type ore can be formed, which is a refractory ore.
The main reason why this type of ores are difficult to separate is that both calcite and fluorite are calcium-containing minerals with similar surface physical and chemical properties. The mutual transformation between minerals is easy to occur when the solution coexists, and the selection of appropriate collectors and inhibitors is the key to the separation of fluorite and calcite.
To achieve the separation of calcite and fluorite, the pH value of the slurry must be adjusted, and then a collector can be used to achieve a good separation effect. In the pH range of 8 to 9.5, using fluorite low-temperature collector ZN136 as the collector, both ores can float, but in weakly acidic medium, calcite has lower floatability than fluorite. Water glass, salted water glass, acidified water glass, sodium hexametaphosphate, lignosulfonate, dextrin, tannin, calcium carbonate special inhibitor, etc. are used alone or in combination to inhibit calcite, so as to achieve the purpose of separation. In actual production, the appropriate chemical system and flotation conditions should be determined according to the specific ore properties through tests.
Calcite-fluorite type ore beneficiation process: raw ore crushing - grading - jig - grinding - roughing - multiple separations;
3. Sulfide fluorite ore flotation
In actual production, the beneficiation technology of sulfide fluorite-type ore is mainly based on the flotation method. First, the sulfide ore is preferentially floated with xanthate collectors, and fluorite is the flotation tailings that are treated as fluorite ore separately. Use fatty acid agents for many selections.
When classifying such ores, sulfide ore collectors are generally used to preferentially flotation metal sulfide minerals, and then fatty acid collectors are used to classify the flotation tailings to recover fluorite.
In order to better extract valuable metals and decompose fluorite, sometimes, in fluorite flotation operations, a small amount of sulfide ore inhibitor (such as cyanide) is added to inhibit residual sulfide to ensure the quality of fluorite concentrate.
In addition, beneficiation technologies such as roasting and leaching can also be used to extract valuable metals and decompose fluorite. The process flow is relatively simple, and high-quality fluorite products can be prepared while comprehensively recycling valuable metals.
Sulfide fluorite type ore-- Ore crushing - grinding - preferential flotation of sulfide minerals - tailings flotation of fluorite - fluorite rough concentrate has been separated many times.
4. Barite-fluorite ore flotation
The main minerals of barite-type fluorite ore are barite and fluorite, and the content of barite is generally 10%-40%, often accompanied by pyrite, galena, sphalerite and other sulfide minerals.
This kind of ore beneficiation is generally mixed and flotation to obtain a barite-fluorite mixed concentrate, and then the separation of barite and fluorite is carried out. According to the order in which barite and fluorite emerge, it can be divided into two schemes:
- Inhibiting barite flotation to fluorite, this method can obtain high-grade barite concentrate and fluorite concentrate;
- Inhibiting fluorite flotation barite, this method first obtains barite concentrate, adds fatty acid collectors and sodium silicate to the tailings, and selects fluorite concentrate several times (7~9 times). The process of this method is simple, easy to operate, and qualified barite concentrate can be obtained, but the grade of fluorite is often not high.
In actual production, the separation of fluorite and barite mostly adopts the process of inhibiting barite with pumice fluorite, and uses fatty acid flotation reagents as fluorite collectors, caustic starch, dextrin and other organic inhibitors. It is used in combination with inorganic inhibitors such as water glass, aluminum salt and iron salt to achieve the purpose of separating fluorite and barite.
The above four types are common fluorite ore types, and the specific beneficiation process is configured according to the actual situation. The complete set of equipment for fluorite ore flotation process is completed, the capital spent is reasonable, and the rate of return is efficient. The process is smooth, one link is linked to another, the steps are compact, and it has been tested and practiced many times. JXSC Mining Machinery can customize various types of fluorite ore process and process design for different users, with 37+ mineral processing experience, safe and reliable, contact our professional engineers for consultation.